- AS-Interface
- Application
ASi-5 AT SPAX: (FUTURE-) SAFE SOLUTIONS
SPAX International GmbH & CO. KG is part of the corporate group ALTENLOH, BRINCK & CO and specialized in modern connection technology. The name SPAX has for over 50 years stood for „Made in Germany“ quality. Around 500 employees near Ennepetal, a city next to the Ruhr area, are involved in producing up to 50 million screws per day, making the company with its familiar green packaging the market leader in Europe and a premium brand around the world.
Everyone knows the SPAX screw, which is offered in countless variations and sizes. But how and with which machines are they produced? The manufacturing process of a SPAX screw begins with cutting pieces of the original material to length from a rolled wire coil. The head of the screw is then formed in a press and compression process. Here the head type is also determined, e.g. Philips-tip. Then the thread and tip are rolled onto the so-called press nail. Finally the screw is hardened and coated before it can make its way to the customer.
Quality with (future-) safety: Retrofit with AS-Interface from Bihl+Wiedemann for presses and rollers
In the production of their screws SPAX uses a variety of identical or similar machines – presses and rollers that were made as early as the 1970’s and 1980’s, but which are so solidly constructed that they are simply mechanically and electronically refurbished at regular intervals to bring them up to the latest technological state. Here the company has its own in-house mechanical engineering group with its own personnel for upgrading between eight and twelve machines per year.
Since presses and rollers are machines whose operation can be inherently hazardous to workers, the subject of machine safety has played an important role right from the start. Compared with the 1970’s and 1980’s, when for example two-hand relays were the norm, safety requirements have in the meantime been significantly enhanced. This is why over ten years ago, SPAX had sought a solution for implementing safety technology in a way that meets current requirements, that is future- and expansion-secure, and which takes up as little physical space as possible – since with 70 to 80 presses and the associated control cabinets space alone is a decisive criterion.
They found what they were looking for at Bihl+Wiedemann, specialists in automation solutions with AS-Interface and ASi Safety at Work. The Mannheim-based company convinced Sascha Roloff, Head of Maintenance at SPAX and his team not only with its safety technology solutions and ease of wiring of standard signals, but also through its expert on-site assistance and technical support. “It became quickly clear to us that Bihl+Wiedemann outside sales people are not peddlers, but rather full-fledged application engineers,” says Roloff. “We got expert support in all matters and decisions from the very outset, and in a relatively short time developed a solution that met our requirements perfectly.”
Safety first - one solution for many machines
Safety technology plays an important role in various places with the machines used at SPAX. On the machine itself it is important that operators can only open guard doors and covers if all potentially hazardous motion has stopped. This is guaranteed on one hand by the ASi Safety Active Distributor (BWU3565) in IP67, which is mounted directly to the machine and which is used to simply, quickly and safely integrate the safety door switch into the ASi network using the familiar profile cable. On the other hand, safe monitoring of standstills takes place. This is accomplished either using a Safety Basic Monitor (BWU2700 or BWU2852) or a Safety Gateway from Bihl+Wiedemann, each of which can be mounted in the control cabinet. Other safety-related tasks that the ASi Safety Gateway can perform include two-hand operation of the presses and rollers as well as the connection of E-Stop buttons.
For SPAX safety technology using ASi Safety at Work has a number of benefits even beyong the simple, flexible and cost-effective wiring technology. Since the majority of the presses and rollers are nearly identical and differ only in slight configuration variants that can be enabled separately, the solution for one machine is transferrable to the others. This means first that as a rule for all the machines can be used the same products with the same functionality at the same location. And secondly, control cabinets can be fully constructed and tested in advance, making it possible to store them ready-to-use. When a machine has then been mechanically and electronically overhauled, the control cabinet can be simply connected up, saving an enormous amount of time. Thirdly, this means that once the safety program for a machine has been saved in the ASIMON360 software suite, it can be easily copied for use in other machines. Finally, the result is that things are made quite easy for personnel who are responsible for maintenance and modernization of the presses and rollers, for example when it comes to troubleshooting. Why? Because they can apply the knowledge about ASi and ASi Safety learned in regular training courses with Bihl+Wiedemann outside sales persons directly from one machine to another. “The cooperation from our colleagues at Bihl+Wiedemann that we have experienced here in the SPAX electronics workshop is really something special,“ says Sascha Roloff. “Regardless of whether we’re bringing our people up to speed on the newest state of AS-Interface, working together on the best solution, or testing new developments – such a partnering relationship from both sides and the advances made are something one seldom experiences.“
In addition to safety technology, another topic solved by AS-Interface was the monitoring of pressure, temperature and flow. Especially when it comes to presses and rollers, where proper lubrication of the machine is always critical for efficient functioning and to prevent damage, these parameters need to be continuously monitored. Here the decision was made early to employ the ASi digital modules from Bihl+Wiedemann, since they can be used in parallel with the safety technology on the same cable and monitored via the same ASi gateway.

ASi-5 und OPC UA: Ready für Predictive Maintenance und Industrie 4.0
How foresighted the decision was to use AS-Interface for the safety technology and the monitoring of pressure, temperature and flow became evident in 2019. It was then that SPAX made the decision to make their production Industry 4.0 capable. In this context the maintenance department at SPAX was also given the assignment to develop a concept for making the presses and rollers ready for Predictive Maintenance. The goal was to get more information from the machines about their condition and feed this information into an IT solution using a standardized protocol so that the current condition of the machine and, when needed, any action recommendations could be derived. Ideally this would involve as few modifications to the existing configuration of the presses and rollers and their control cabinets as possible. After deep-diving discussions and tests a solution was developed together with Bihl+Wiedemann that could be implemented while meeting nearly every formulated requirement. A contributing factor was that at the end of 2018 with ASi-5 the newest AS-Interface generation was brought to the market, which is downward compatible with all previous ASi generations, has the necessary high data bandwidth and short cycle times for sending even the data from IO-Link sensors. In addition, Bihl+Wiedemann has in the meantime equipped all their new ASi gateways with an OPC UA interface for making the data directly accessible to the IT while bypassing the controller.
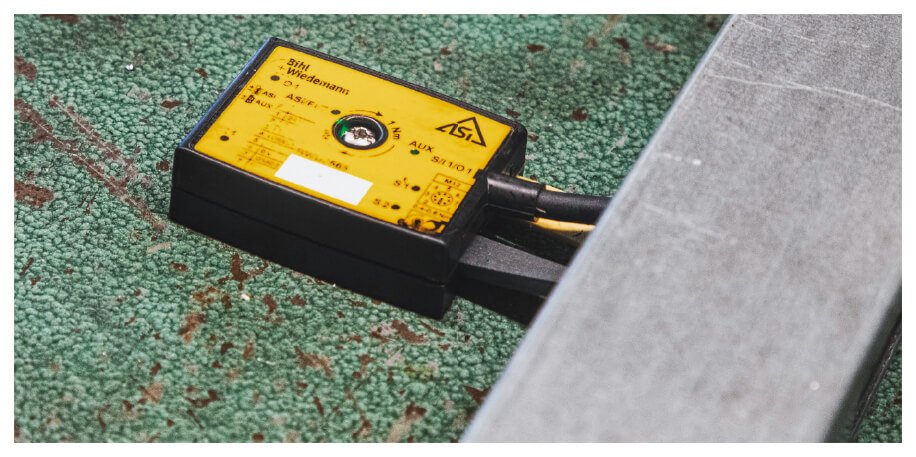
What does this mean in detail for the presses and rollers at SPAX? The complete safety technology can be left just as it was – simply the previous ASi Safety Gateway has to be replaced with the ASi-5/ASi-3 PROFINET Gateway (BWU3863) including its integrated safety monitor and OPC UA server. The configuration effort required is extremely minimal. And instead of the ASi digital modules, now the ASi-5 Modules (BWU4067) with integrated IO-Link Master with four Master Ports are used and connected to the already installed IO-Link compatible sensors for pressure, temperature and flow and are likewise parameterized using the ASIMON360 software. These few and simple changes now make predictive maintenance possible, since the connected IO-Link devices no longer provide just digital values, but rather process and diagnostic data as well which are send to the IT through the OPC UA server in the ASi-5/ASi-3 Gateway. This allows SPAX for example to recognize early whether and how the pressure, temperature and flow are changing and react as needed to prevent expensive machine downtimes or even damage.
As far back as 2020 SPAX began to make the first machines “ready for predictive maintenance“ in line with the commonly developed solution, and since then retrofitting of the presses and rollers is proceeding step by step. And after this already so successful cooperation, Sascha Roloff can already say: “When the next large project involving robotics applications is coming up, we will again be relying on the solutions of our partner Bihl+Wiedemann.“