- AS-Interface
- Technology
COMPACT SAFETY CONTROLLER WITH GROWTH POTENTIAL
Implementing functional safety simply and cost-effectively, regardless of the controller or fieldbus used and both scalable and
future-proof is the basic starting point of the AS-Interface wiring technology. The ASi-5/ASi-3 portfolio from technology leader Bihl+Wiedemann offers all the options for such efficient solutions. Many users “start small” with the Safety Basic Monitor, for example, to initially use only its configurable safety relay functionality.
If the applications and requirements grow, then the compact safety controller can also grow with its tasks - up to the full scope of performance with up to 31 connected safety modules. These can be simple safe in- or output modules as well as specialized modules for safe speed, position or analog value monitoring as well as for muting applications. The Safety Basic Monitor can then for example be used as
the head station for distributed safety applications in modular machines or on driverless transport systems. Whether small or complex – this compact safety controller as well as the overall safety solution can be conveniently configured, parameterized and tested using the ASIMON360 PC software from Bihl+Wiedemann.
Small, configurable, cost-efficient: the Safety Basic Monitor
The compact safety controller Safety Basic Monitor with integrated safety monitor from Bihl+Wiedemann has an installation width of just 22.5 mm which makes it perfect for space-saving DIN rail mounting in control cabinets. In addition to two electronic, safe semiconductor outputs, it provides up to four safe two-channel inputs or up to eight digital I/Os depending on the configuration. Also included are the basic functions of safe motion monitoring: safe two-channel standstill monitoring up to SIL2/PLd as well as safe speed monitoring for two or four axes that meets SIL1/PLc for a single channel or SIL3/PLe for two channels. Equipped with a variety of additional functions, for example for connecting
light barriers, two-hand switches or door interlocks, the Safety Basic Monitor is a cost-effective solution for small applications – especially since such safety devices can be connected quickly and with reverse polarity protection via two-core profile cable using piercing technology. As a configuration and diagnostic interface the Safety Basic Monitor offers optionally an Ethernet TCP/IP or USB interface.
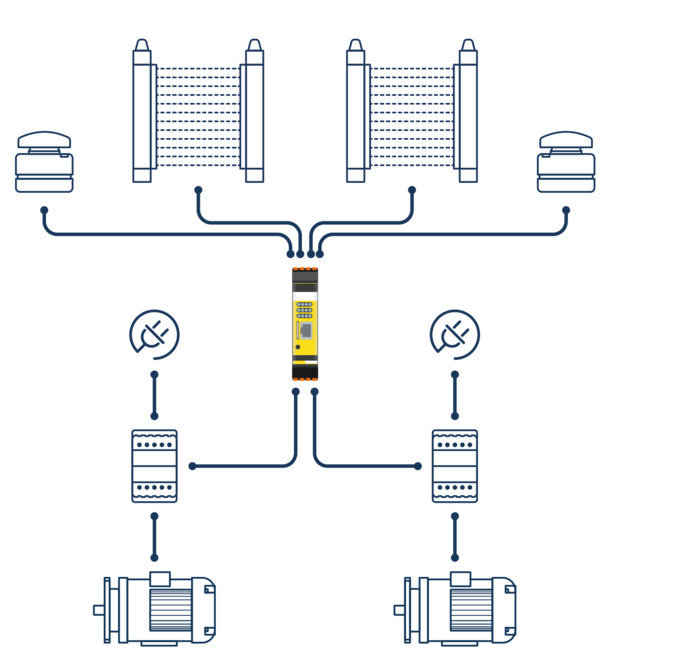
ASi Safety provides additional functionality
When used together with the integrated ASi Master and ASi Safety Monitor, the Safety Basic Monitor can process up to 31 safe signals through additional safe in- and outputs. The sensor-supported monitoring functions for speed and standstill which are already available in the stand-alone version are supplemented with additional special applications when integrated into ASi Safety. This compact safety controller can directly accept and process the signals from special safety speed monitors for encoders which provide additional safety functions.
This means you are not limited to standstill and speed – now you can also monitor speed ranges, speed direction, positions and position ranges, end positions or braking ramps. Also, malfunctions such as slippage, misalignment or shaft break can be reliably detected. As an ASi Master with integrated safety monitor, the Safety Basic Monitor can also be used for safe transmission and processing of analog values, such as in the safe monitoring of temperature, pressure or position.
And finally, this compact safety controller can be combined with ASi Safety to implement material handling functions such as muting – the temporary bypassing of an optoelectronic access protection using muting sensors in the stationery material flow – or gating – the automatic, momentary bypassing of a non-contacting protection device without muting sensors.
Integrated Safe Link connection enables safe coupling over Ethernet
Another way to expand the range of applications is to combine the Safety Basic Monitor, which itself has only a Modbus TCP connection for diagnostic purposes, with other safety controls. These safety controls can also be Safety Basic Monitors, but also ASi-5/ASi-3 fieldbus gateways from Bihl+Wiedemann with ASi-5 and ASi-3 safety technology. These gateways not only allow safe signals and standard data to be collected and sent to the PLC over a fieldbus. There are also versions for safe fieldbuses and with FSoE master and CIP Safety Originator functionality that can be used to directly parameterize and control safety drives.
The Safety Basic Monitor as well as all the ASi Safety gateways from Bihl+Wiedemann use their Ethernet diagnostic interface to provide safe coupling with each other – without any additional expense or hardware such as a safety PLC.
Using this technology – called Safe Link – safe networks such as various system components or driverless transport systems can be connected to each other – even when using different controllers. This puts Safe Link fully in the vanguard, because in both factory and process automation the number of complex, branched applications is growing – and with them the safety technology challenge of efficiently coupling these networks with each other. Information exchange can take place both hardwired over the Ethernet diagnostics interface or wireless, for example via radio data transmission, data light barriers, 5G or in industrial WLANs.
Regardless of the size of the plant, Safe Link sub-systems can be combined into a larger overall system. Up to 31 Safety Basic Monitors or gateways with integrated safety monitor can be coupled with each other – without sacrificing performance and without the need for additional hardware. In the maximum configuration with up to 62 safe I/Os per gateway nearly 2000 safe signals can be exchanged to handle virtually any application.
The Safe Link technology thereby meets the highest safety requirements up to SIL3/PLe. Complex plants can first be constructed independent of each other as individual machine segments, then equipped, tested and approved with the Safety Basic Monitor or an ASi-5/ASi-3 gateway for safety, and the modules later coupled to each other and placed in operation as an overall system. Once the system is running, everything is possible, from direct (unicast) communication between each device and a central manager to broadcast operation according to the principle that each device communicates with all other devices.
The Safe Link technology thereby meets the highest safety requirements up to SIL3/PLe. Complex plants can first be constructed independent of each other as individual machine segments, then equipped, tested and approved with the Safety Basic Monitor or an ASi-5/ASi-3 gateway for safety, and the modules later coupled to each other and placed in operation as an overall system. Once the system is running, everything is possible, from direct (unicast) communication between each device and a central manager to broadcast operation according to the principle that each device communicates with all other devices.
Safe, physically compact but large in range of functions and with potential for even more – the Safety Basic Monitor lets you handle small standalone applications cost-efficiently. Yet when combined with expanded functionalities provided by ASi Safety and Safe Link it offers all the possibilities for handling even safety-relevant requirements in complex systems reliably and ready for whatever the future brings.