AS-Interface – Automation made simple
What is AS-Interface?
AS-Interface (ASi) is a globally standardized fieldbus system for the first level of automation. The abbreviation ASi stands for Actuator-Sensor Interface. ASi connects sensors and actuators with a controller via a single two-core profile cable. The yellow ASi cable transmits power and data at the same time. The main advantages of AS-Interface are, among others, dramatically less wiring, free choice of topology and cost-efficient integration of safety on the same infrastructure.
The latest ASi-5 generation can now handle larger data volumes at much higher transmission speeds and it enables intelligent sensors such as IO-Link to be integrated with ease.
Content
- What is AS-Interface?
- ASi-5 – The latest generation of AS-Interface
- Data and power on one cable
- AS-Interface components
- Wide range of applications of AS-Interface
- AS-Interface software
- Advantages of AS-Interface
- ASi Safety at Work
- FAQ about AS-Interface
- ASi-5/ASi-3 Address Programming Device – Simple for all ASi generations
Advantages of AS-Interface
AS-Interface reduces cabling and assembly costs to a bare minimum, and is extremely easy to expand or retrofit. ASi enables fast and flexible installation in which new bus devices can be connected without complex cable configuration.
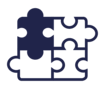
Independent of system and manufacturer
The ASi technology is compatible with almost all common fieldbus systems. It does not matter whether PROFIBUS, PROFINET, CC-Link, EtherNet/IP etc. are used at the higher levels.

Save valuable resources
With AS-Interface, you do not need expensive plugs or sockets and only a single cable. This significantly reduces assembly times and material costs. In addition, valuable resources such as copper or plastic, which are required to manufacture the components, can be saved on a large scale. And energy consumption during cable production is greatly reduced. There is also a positive environmental effect when it comes to disposal – less waste is produced.
Data and power on one cable
ASi connects the modules in the lowest process level in automation systems with each other. The usual cable harnesses are replaced by a single electrical cable – the ASi cable. Both data and power are transmitted on this one cable.
Extremely simple installation, perfect contacting
Thanks to ASi piercing technology, it is possible to connect, replace, move or add modules - e.g. ASi-5 modules with integrated IO-Link master with 1, 2, 4 or 8 ports. Benefits when using the profile cable include the following:
- Very simple connection technology: Modules pierce the insulation of the profile cable. At least four gold-plated needles pierce vertically and reliably through the rubber sheath into the cable, where the two cable wires come into contact.
- Maximum safe contacting: Two needles per wire penetrate the profile cable redundantly. Low contact resistance is also guaranteed.
- Reduced installation effort: There is no need for cutting or stripping and terminating the cable as with round cables. The profile cable is simply taken from the cable reel in the desired length.
- Zero Euro connection costs: Neither pre-assembled cables nor T-pieces are required to connect modules. This makes the retrofitting or conversion of systems unrivaled in terms of cost.
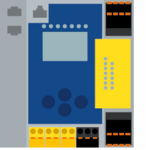
AS-Interface Master
The ASi Master organizes the data traffic on the ASi cable and connects sensors and actuators to the higher level control.
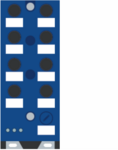
AS-Interface node
ASi nodes connect sensors and actuators to the ASi cable. There is a suitable ASi node for almost any conceivable application.
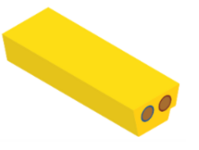
AS-Interface cable
The yellow ASi cable connects the ASi Master and transmits data and power on two conductors. Thanks to ASi piercing technology, modules can easily be connected, replaced, moved or added.
More and more companies across different sectors are now choosing ASi solutions from Bihl+Wiedemann to automate their plants and systems. The open bus system is particularly widespread in factory and industrial automation, conveyor applications, building automation and mechanical engineering.
AS-Interface software
Various software products are available for simple commissioning, configuration and diagnostics of ASi networks.
ASi-5/ASi-3 Address Programming Device – Simple for all ASi generations
With the compact ASi-5/ASi-3 address programming device, you can easily commission ASi modules of all generations - including ASi-5 modules.
- Supports ASi modules of any generation, incl. ASi-5
- Optimized for simple addressing without additional mobile terminal devices
- Six solidly designed buttons for simple operation
- Modern OLED color display
- Standard USB-C port for power supply and as PC interface
- Modern power storage (supercapacitors) for fast charging and longer lifespan
- Charging time: fully charged in approx. 30 min, sufficient for 120 read/write operations, already 10 min of charging are sufficient to allocate 70 ASi addresses (e.g. AB, single, ASi-5)
- Ready for use even after months of storage thanks to low self-discharge
ASi Safety at Work
Thanks to the ASi Safety at Work concept, it has been possible to seamlessly integratesafety-related components, such as safe sensors, actuators and safety monitors, into almost all popular automation systems. ASi Safety at Work is approved for applications that must meet safety requirements up to SIL3 in accordance with EN 61508 or PLe in accordance with EN ISO 13 849-1:2006.
ASi-5 – The latest generation of AS-Interface
The new generation of AS-Interface now enables significantly faster transmission of larger volumes of data and simple integration of intelligent IO-Link sensors. For example, ASi-5 enables fast transmission of up to 32 bytes of IO-Link process data via ASi. As a result, many things that were previously not possible with AS-Interface are now possible.
The AS-Interface master connects sensors and actuators to the higher-level control via the ASi modules. With the ASi Master, digital and analog data that has been gathered decentrally by ASi modules, can be transferred to the higher level control through the respective bus system. The output signals of the controller are transmitted then through ASi to the actuators in the field.
ASi nodes are connected to the ASi Master with a cable. They are used to integrate the sensors and actuators into the ASi network, regardless ifinside the switching cabinet or in the field. These are connected to the power supply and data communication in the ASi network. Each node is assigned to a unique address in the network.
The ASi cable is an unshielded, 2-core cable. It not only transmits data and power, but also enables easy and cost-effective installation. Thanks to piercing technology, participants can easily be installed on the profiled (thus reverse polarity protected) ASi cable – with perfect contacting and achieving protection class IP67. An additional 24 V supply is possible without problems.
An ASi wire stripper is used for stripping ASi cables with an outer insulation of thermoplastic elastomer (TPE) or polyurethane (PUR).
The sensors or actuators are usually connected by means of piercing technology. In this process, the insulation of the flat cable, which is profiled to protect against reverse polarity, is pierced during installation by two piercing pins without the cable needing to be prepared beforehand. In this way, nodes can be relocated or added directly on the cable at any time without major installation effort.
Addressing of ASi-3 nodes
With ASi-3, there are 31 ASi addresses available, whereby each address may only be allocated once. A distinction is made between standard addressing and extended addressing. The addressing mode of ASi participants is determined by the manufacturer. With standard addressing, each ASi participant reserves a full address (1..31). With extended addressing, each address can be reserved by two ASi participants (1A..31A, 1B..31B). It is not possible to address an ASi node with standard addressing and an ASi participant with extended addressing on the same address, e.g. 3 and 3A or 3B.
Addressing of ASi-5 nodes
With ASi-5, the nodes are assigned an ordering number starting from 1. The numbering takes place sequentially.
In conventional design, a separate ASi power supply (with integrated decoupling coils) is required for the voltage supply of each ASi circuit. With ASi gateways and safety monitors of the version "1 power supply, 1 gateway for 2 ASi circuits, cost-effective power supplies" by Bihl+Wiedemann, the decoupling coils are already built into the devices. This enables the supply of two ASi circuits by means of one standard 30 V power supply.
With short cable lengths, even a standard 24 V power supply can be used. This is an optimal solution for small and very small systems – i.e., for small machines with 3 to 15 ASi nodes and a maximum cable length of 50 meters. We have an affordable line of ASi gateways, optimized for 24 V applications.
ASi distributors enable simple connection of various sensors and actuators to ASi anywhere in the field over an M12 connection. Active distributors are required for sensors and actuators without an integrated ASi chip. Passive distributors are suitable for sensors and actuators with an integrated ASi chip.
For mixed ASi-5/ASi-3 circuits, we recommend an additional ASi bus termination if the cable length is approx. 70 m or longer. The ASi bus termination can help improve the ASi-5 communication.
The total length of the ASi standard network is limited to 200 m for ASi-5 and 100 m for ASi-3. To determine the total length, all junctions must be included in the calculation. The ASi repeater is a module for cable extension. It makes it possible to increase the cable length in an ASi-3 network up to 200 m. Areas with strongly impaired EMC can thus be bypassed. ASi repeaters cause a certain delay in the transmission of telegrams.
This diagram shows the basic structure.
ASi-3 is a proven and stable technology with a wide range of available products. However, ASi-3 continues to be a future-proof technology whose possibilities are far from being exhausted. In the course of digitalization and Industry 4.0, it is now necessary to retrieve more and more data more quickly from the field level - in order to subsequently process them in higher-level instances. ASi-5 was developed for this requirement: The latest ASi generation offers a correspondingly high data bandwidth and short cycle times.
ASi-3 and ASi-5 are compatible with each other and complement each other optimally. Depending on the application or requirement, it must be checked individually which ASi technology is when the most appropriate or most economical. In practice, there will mostly be applications in which both ASi technologies are used. ASi-5 will therefore not replace ASi-3.
ASi end caps are used to protect the bare ends of the ASi or AUX profile cable against dust and humidity up to max. IP67 – for interference-free communication in the ASi circuit. They are available as left and right versions. Many Bihl+Wiedemann nodes and active distributors do not generally require the use of end caps because the cable ends can be terminated in the base.
How to extend the ASi-3 cable to, e.g., 1,000 m
Extend the range of the ASi circuit flexibly and cost-effectively. Learn more about the possibilities of cable extension.
Connect any sensors and actuators to ASi
With the help of passive distributors from Bihl+Wiedemann, any sensors can be integrated into an ASi network.
ASi modules for use under extreme conditions
Here you will find an overview of our modules in the EXTREME product category for use in extreme conditions.
ASi for a wide range of applications
Learn how you can use AS-Interface in building automation, packaging automation or material handling.